Steel and aluminum prices have jumped sharply since the turn of the new year, and more volatility could be on the horizon.
Contractors are bracing for a new wave of tariffs set to take effect April 2, this time on certain material imported from Canada and Mexico — such as steel, aluminum and lumber. Though reports indicate the Trump administration could roll back the ultimate scope of this action, contractors say just the threat of tariffs can have an immediate impact on material costs.
That’s why that looming deadline on Canadian and Mexican imports has already sparked concern across the construction industry, particularly around reinforcing and structural steel, curtainwall systems and Canadian lumber, said Steve Stouthamer, executive vice president of project planning for Skanska USA Building.
Here, Stouthamer talks with Construction Dive about the materials most at risk, tariffs’ impact on budgets and negotiations and steps contractors can take to minimize financial exposure.
This interview has been edited for brevity and clarity.
CONSTRUCTION DIVE: Which construction materials do you expect will see the greatest price volatility due to tariffs?
STEVE STOUTHAMER: The materials being impacted the most are products made from steel and aluminum.
For example, reinforcing steel used in concrete, structural steel used in the building frame, aluminum curtainwall and window wall systems used in the building envelope, piping and ductwork used in mechanical and electrical systems and many building mechanical and electrical equipment components.
Steel prices have increased 15% to 25% since the beginning of January and aluminum is also up 8% to 10% from the beginning of January. The Trump administration has indicated Canadian lumber will be included in the reciprocal tariffs which are set to take effect on April 2. Lumber has already seen a significant increase, 10% to 15% in cost, in anticipation of this tariff.
How might these tariffs affect project costs and timelines?
We are in the early stages of helping our clients understand the order of magnitude cost impacts we see based on current tariffs and those will vary based on the type of project and the material composition of those projects.
At present, we are not expecting a near-term impact on project timelines. If there is a considerable shift to onshoring manufacturing, supply chain schedules could be constrained, but this is not like the situation we experienced during the pandemic where the supply chains were impacted by global shutdowns.
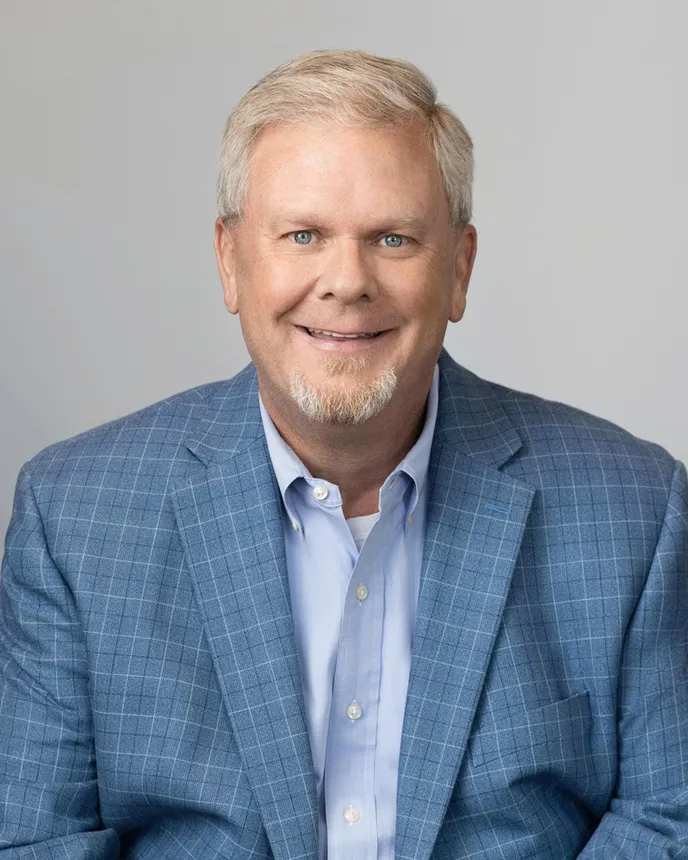
Steve Stouthamer
Courtesy of Skanska USA Building
At the moment, the broader Mexico and Canada tariffs on products protected by the United States-Mexico-Canada Agreement are suspended until April 2. Upon resumption, it is our current understanding that 25% broad tariffs on all goods from Mexico and Canada would stack on top of the all-country steel and aluminum tariffs of 25%, resulting in a 50% levy.
With the latest tariff suspensions, it is unclear if this will ultimately be the case. We will be monitoring the situation in the weeks ahead.
How do you see tariffs affecting negotiations with owners and developers?
Tariff cost impacts will put pressure on project budgets. Many of those are already challenged by the significant period of escalation experienced post-pandemic.
We are only a few weeks into the tariff executive orders so it’s too early to comment with certainty as to how contracts will be impacted or negotiated. Our approach will be to engage with our clients and discuss the most cost-effective ways to manage the tariff risks.
Do you expect issues with tariffs to be temporary or a long-term factor that construction firms need to adapt to permanently?
It’s too early to comment on this.
History would suggest that even when tariffs are removed and trade agreements are reached, costs don’t just return to previous levels.
What policy or industry efforts could help mitigate the impact of tariffs on construction firms?
Estimating professionals will need to take deeper dives into their projects to understand product volumes, sources and tariff impact to assist clients in better understanding the financial impacts of tariffs and potential alternative products and product sources.
Strategic supply chain teams, such as our own at Skanska, will need to remain closely connected to the supply chain and major fabricators of steel and aluminum products as well as other key construction materials that will be impacted by tariffs. It is essential to have this connectivity so that companies such as ours can continue to advise clients and industry partners on the best strategies to mitigate the impact of tariffs.
Projects can benefit by investing additional time into the mapping of the specified materials for the project to determine their source, if those sources are impacted by tariffs and whether alternative products and sources could mitigate financial risk.